Bending
Wallflex panel’s bending through a template is necessary to realize Wallflex shaped panel. This realization starts with the preparation of a wooden template with a curve side, according to the radius that Wallflex shaped panel must finally have. Once that such template is ready, a Wallflex monolayer panel is placed over it, coupling the aluminum layer with the wooden template. A second aluminum layer is then glued on the aluminum corrugated core and the whole shaped panel is fixed to the template. At the end of the gluing process, extremely lightweight and strong Wallflex shaped panel is obtained.
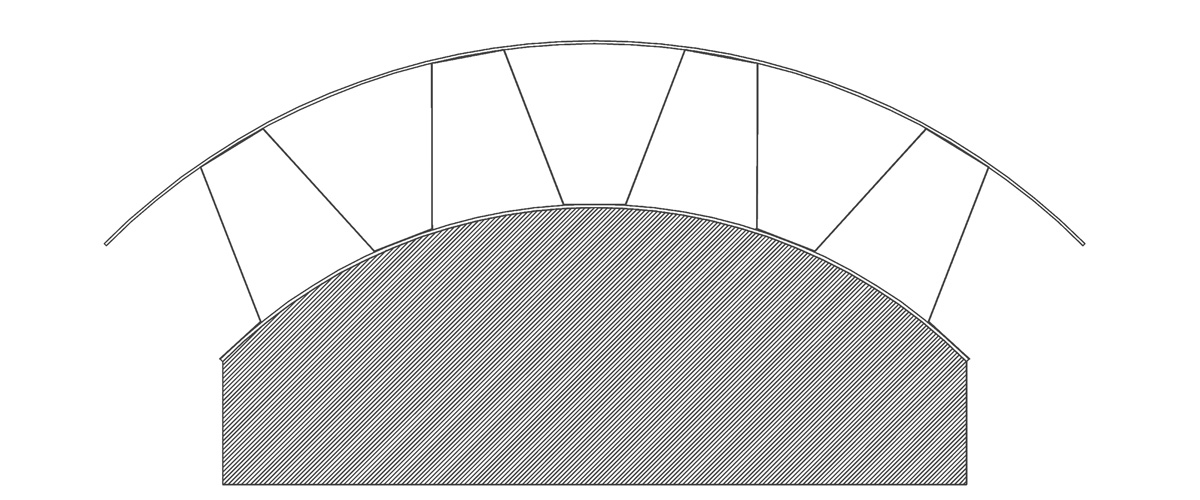
Cutting
Aluminum Wallflex panel can be cut and worked according to specific customer’s requests and it is possible to realize the most various planar geometries.
Panel’s cut and working are made through standard machines, similar to ones used for wood working, and this aspect makes Wallflex panel very workable.
Considering the tight tolerances required for edge bending and bending along Wallflex panels, these are worked on CNC stations.
Aluminum Wallflex panel can be used for box element realization, interior design and closed shapes, thanks to the folding working: starting from a standard Wallflex panel, this is cut according to the right dimensions and geometries in order to achieve the planar development of the box element. Then, some V incisions are made along the folding lines, without cutting the bottom layer, and some glue is put inside these incisions. Then follows the panel bending along the incision, in particular, the bending of the box element’s sides, and then some belts are used in order to keep the final position of the box element during the glue reaction. Finally, a complete 3D object is obtained, composed by a single aluminum Wallflex panel, with a low number of junctions between the sides and the panel itself, and so, structurally stronger.
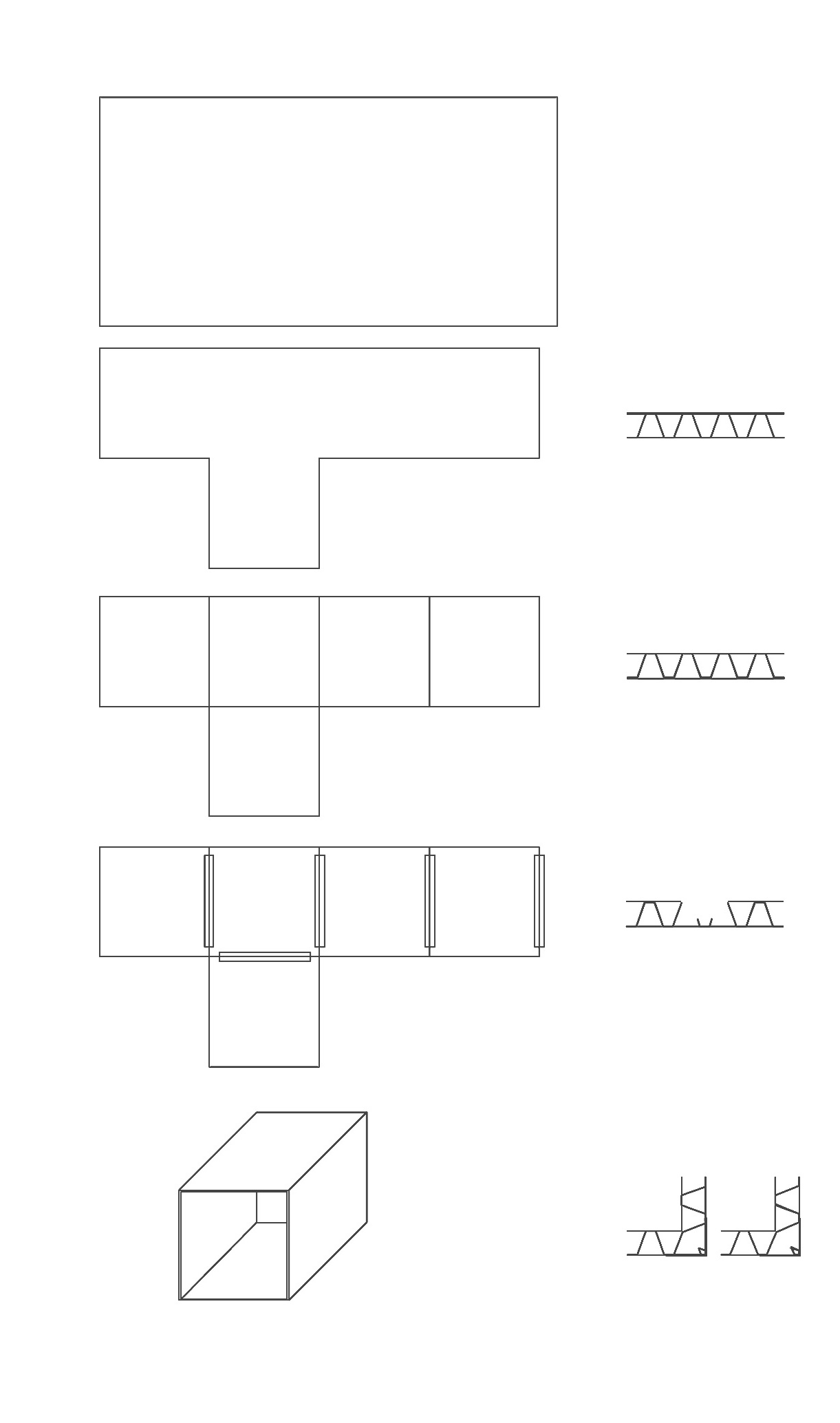
Fixings
Fixing through rivets: aluminum Wallflex panel allows the use of standard rivets or threaded inserts for the junction of two panels or for the fixing of other materials and accessories. Rivets and threaded inserts can be through ones and they can act on both layers or only on one layer.
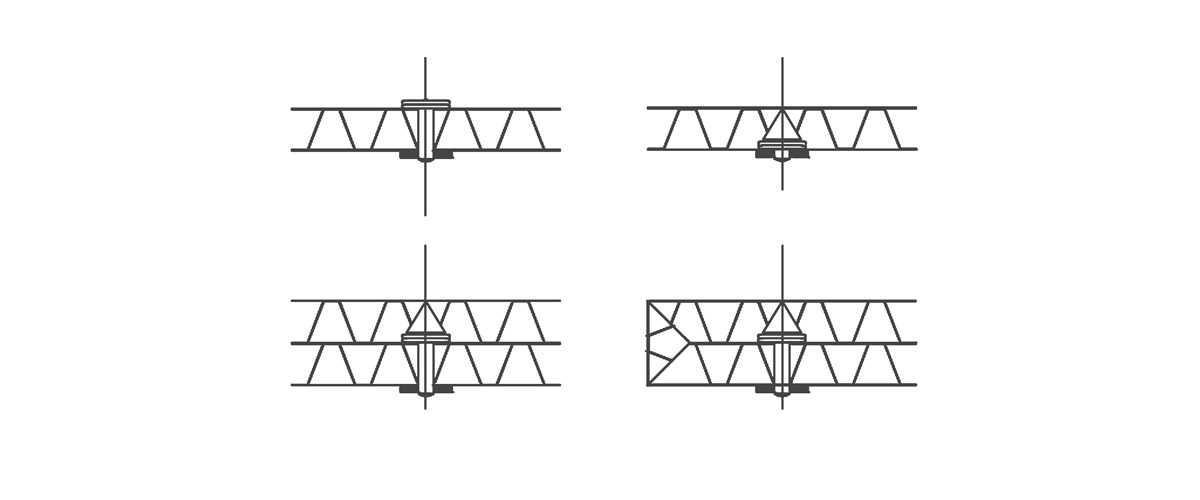
Fixing through screws, nuts and bolts: aluminum Wallflex panel allows the use of standard self-tapping screws.
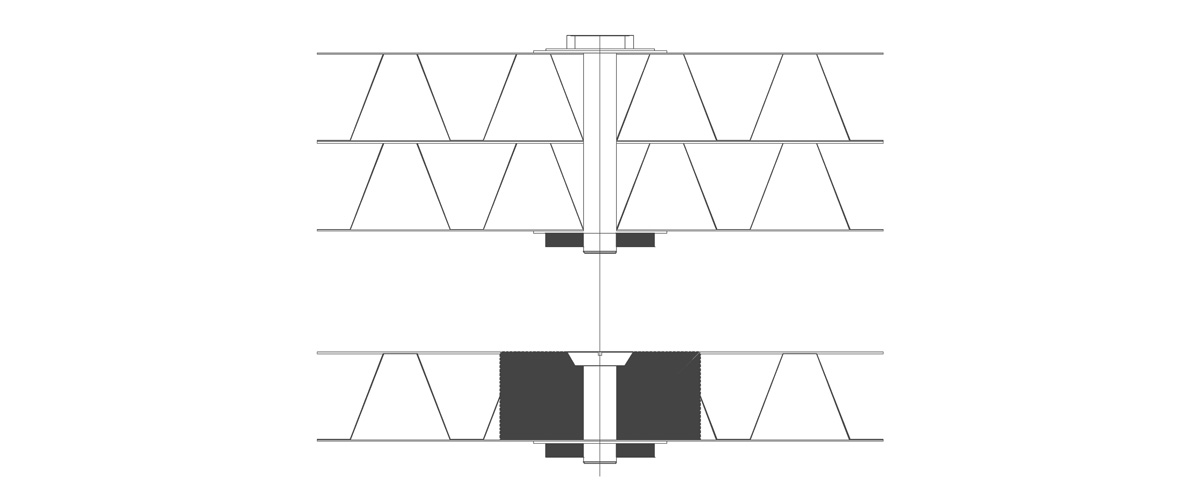
Fixing through gluing: it is possible to realize Wallflex elements by gluing panels together, obtaining an aesthetic cleanliness and avoiding rivets and screws view. Besides, glues have a sealing action against liquids, distribute the loading force, are lightweight and do not modify the element’s geometry. It is also possible to use glue for coupling Wallflex panel to different types of accessories.
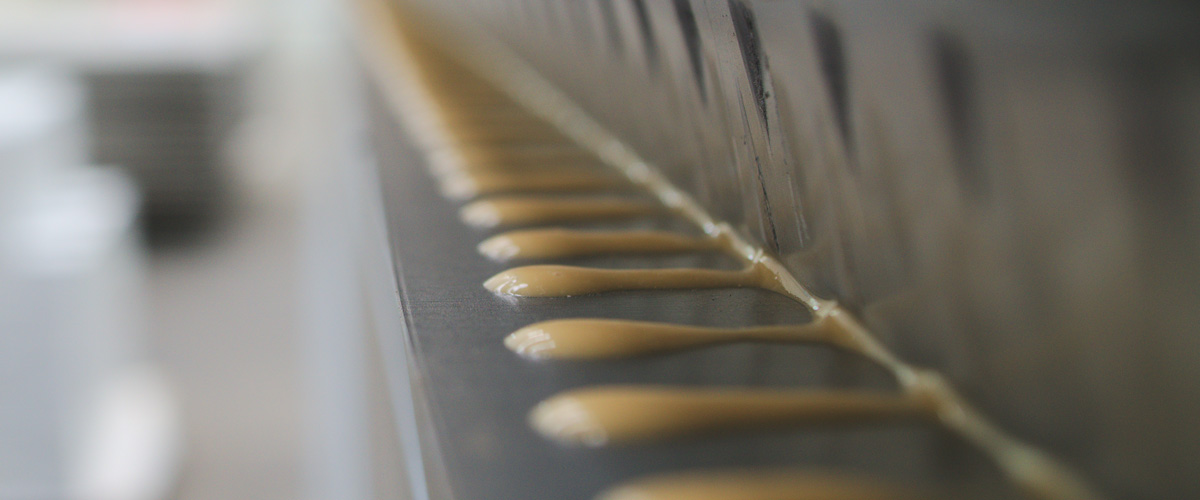
Edging
Edging with aluminum or plastic extruded elements: aluminum Wallflex panel can be edged by using aluminum or plastic-material extruded elements, with I, C or T section, that are fixed at the edge of the panel through glue. Follows pressing.
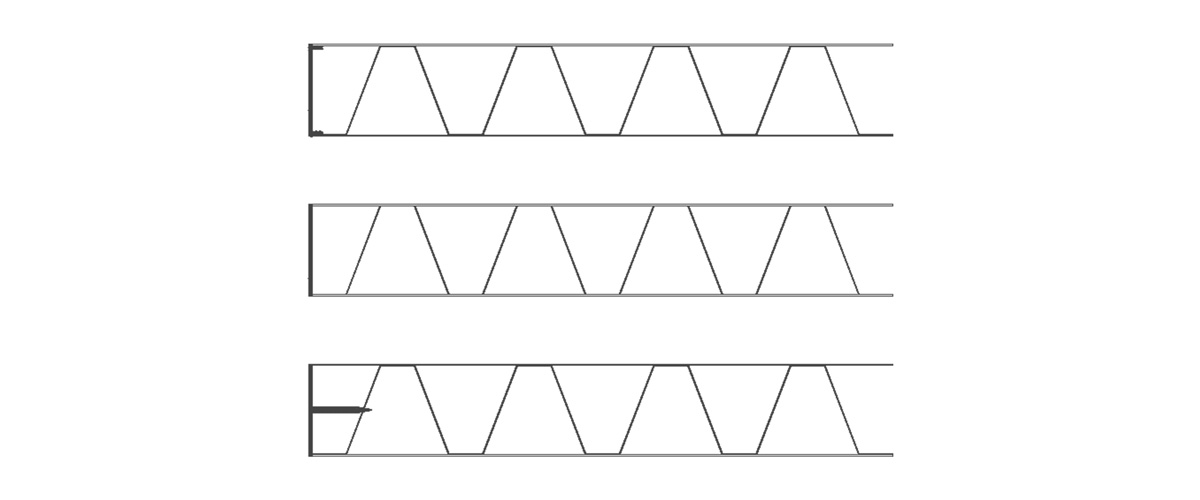
Edging with aluminum or plastic stripes: Wallflex panel can be edged with aluminum or PVC stripes, which are glued on the panel’s edge.
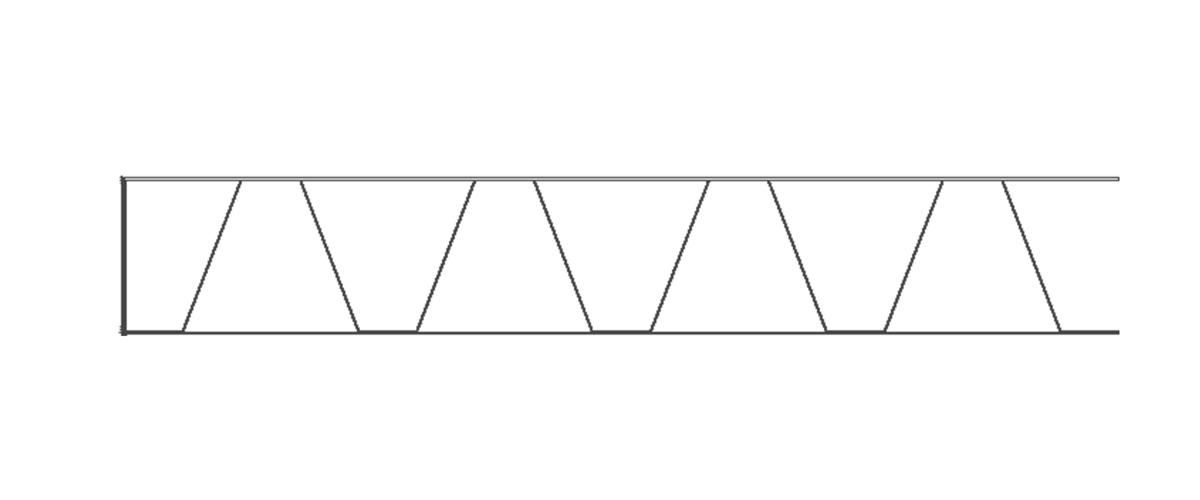
Edging through folded side: in order to achieve this kind of edging, some of the corrugated core is taken away along the edge that has to be folded. Then, a V incision is made on one of the two aluminum layer, the right amount of glue is placed and the incised edge can be bended and folded. Finally, the edge must be kept in position for all the glue’s reaction time. Both the folded layer profile and the non folded layer one are cut at 45°, in order to make the gluing non visible.
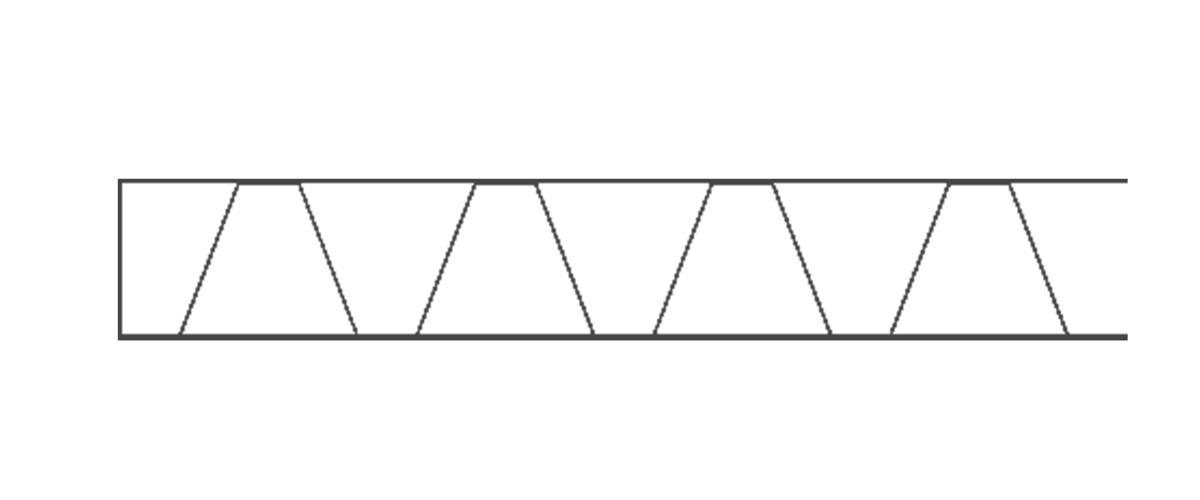
Edging through solid material: aluminum Wallflex panel goes through a partial removal of the corrugated core, to allow the insertion of a wooden solid block, which is coupled to the aluminum panel by glue.
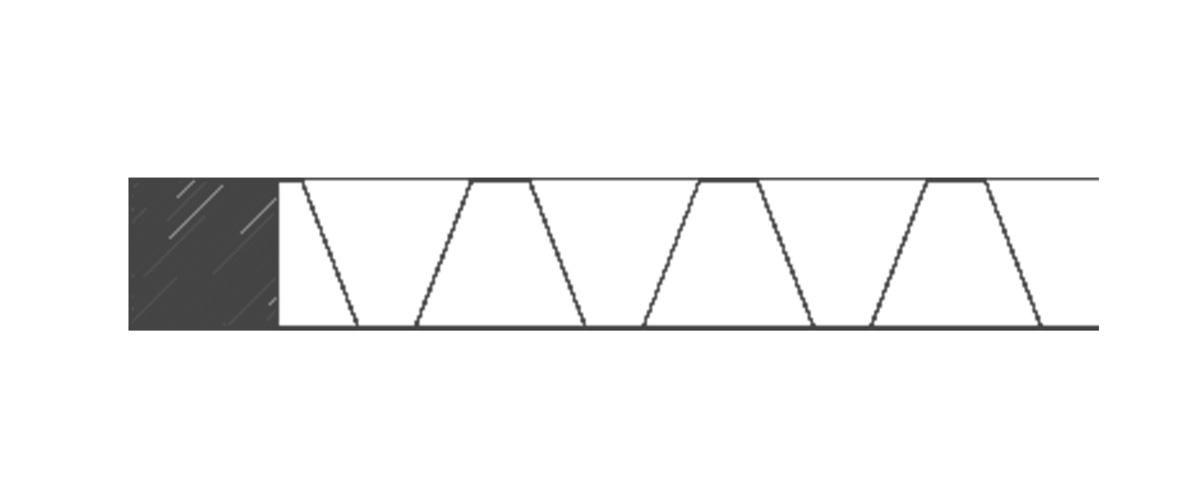
Surface finishes
The panels made by Wallflex can be completed with a surface finish. Aluminum Wallflex panel undergoes to a base anodic oxidation to create a light oxide layer that protects the surface from corrosive agents and that allows a subsequent painting or surface finishes gluing. Therefore, this anodized aluminum panel can be used without further surface treatments.
Among different available surface finishes, there are:
- Liquid painting
- Powder painting
- HPL laminates
- CPL laminates
- Wooden veneer
- Natural or synthetic leather
- Paper or fabric wallpaper
- Tiles, marbles and granites
- Glass
- Solid surface materials
- Fiberglass